Fluicell AB is an innovative company in the area of regenerative medicine, changing the way we treat diseases (like Type 1 diabetes and cardiac disease). Biopixlar AER is their first single-cell bioprinting platform that fits into a biosafety cabinet and is designed to bring you all the power of Fluicell’s open-volume microfluidic bioprinting technology in a streamlined platform built for easy workflow integration.
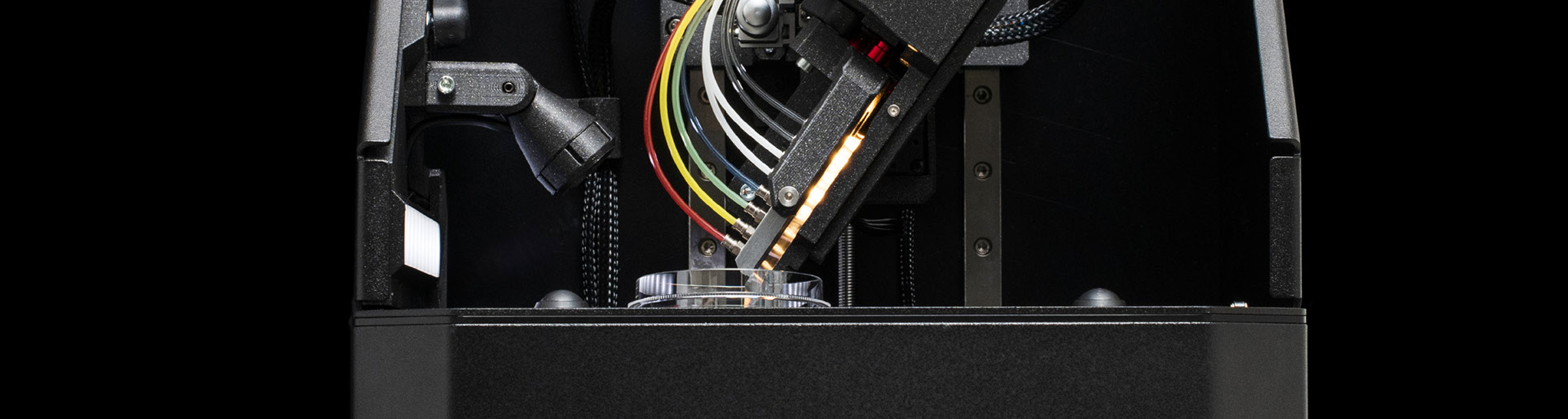
Biopixlar AER instrument
Fluicell AB
Desing 3D bioprinter hardware and software
Fluicell has a patented novel micro-fluidic printhead design and a team of seasoned scientists and experts in developing and commercializing workflows for the pharmaceutical and therapeutics industry. Our challenge in the Biopixlar project was to design and create a custom lab instrument (around this novel micro-fluidic printhead) from the ground up, so it would be easy and fast to operate for the lab personnel. This involved everything from a shell and precision 3-axis motion system and fluorescent microscope design to custom flow controllers and all-in-one desktop software to orchestrate all the sub-systems in the instrument.
Our responsibility was to design complete 3D bioprinter instruments from the idea to instrument that would be manufacturable in mid-size production runs:
- DFM analyzes to make sure the form factor is affordable to manufacture and transport and also is in form-factor that’s suitable for end-users who want to do the installation themselves (during the pandemic, this was especially important).
- Custom PCB design with ARM-based (STM32) for print chamber control.
- 3-axis precision (< 5 um accuracy) motion system (TMC based) + auto-focusing single-channel fluorescence microscope to monitor the open-volume printing process.
- 8-output (4 pressure chambers + 4 x MUX) flow controller to control the cell deposition process.
- Automatic print-head holder (with motorized manifold and tilt-angle control) to make loading cells easier.
- Brushless motorized membrane flow controller (for systems with smaller channels or higher flow rates).
- Windows desktop software (JavaFX + Pyhton and OpenCV) to control all aspects of the instrument hardware + custom visual editor to quickly design print patterns. Just hit print and see the results on the microscope feed!
- Custom CNC and sheet-metal shell design to make the instrument good-looking, self-contained, and easy to move around safely.
- Custom Packaging design (with FEM analysis) to make sure that all the fragile (optics) and sensitive (precision motion system) parts of the instruments are well protected during typical transportation using a courier company.
Impact
We helped Fluicell to bring the idea from sketchbook to a fully functional, manufacturable and deployable form. Currently, the instrument are in active use in diabetes and cardio vascular disease research.